Contact Lenses and
The Work Environment
Studies and organizations find that most patients can safely wear contact lenses in industrial environments if they take proper precautions.
BY JASON J. NICHOLS, OD, MS, MPH, AND GREGORY W. GOOD, OD, PHD
Contact lenses often provide cosmetic and optical advantages over spectacles. Most of the nearly 35 million US contact lens wearers are primarily motivated to wear their lenses by convenience and cosmesis. Contact lens wear can also improve patients' visual, social, psychological and physical functioning. Compared with spectacles, contact lenses also offer increased visual field, decreased glare, reflections and fogging and reduced mechanical interferences. All of these benefits generally outweigh the risks and discomforts associated with potential mild to serious contact lens-related complications.
Some industrial environments, especially those that require safety glasses, reduce or eliminate some of these advantages.
Contact lens wear in the work environment has been controversial for more than 40 years. The controversy is whether the potential for increased ocular risk in specific work environments overcomes the general advantages of lens wear. The type of work environment and the use of protective devices vary markedly among occupations. Some of the many factors associated with occupational ocular risks include exposure to radiant energy (ultraviolet [UV] exposure for welders, infrared [IR] exposure for iron or steel workers), flying particles and mechanical trauma (for construction workers), chemical exposures (for some laboratory workers) and allergenic factors (for gardeners and animal caregivers).
This article reviews research, associated safety regulations and standards and organizations' position statements about contact lens use in different industries.
Research
During the 1970s and early 1980s, research studies attempted to replicate industrial exposures to the eyes of contact lens wearers. Major categories of research examined arc welding, chemical agents, physical agents and foreign bodies and mechanical trauma.
In general, these studies provide evidence that contact lens wear in industrial environments with potentially hazardous exposures is safe when patients wear proper protective ocular devices and when contact lenses do not exacerbate any potential ocular injury.
A 1974 survey reviewed the records of 128 documented cases of eye injuries and/or hazardous exposures that involved rigid contact lens wear. Several of the surveyed doctors suggested that contact lens wear actually provided added protection and minimized the extent of the injury, and no cases existed in which the doctor felt the contact lenses made the injury worse. This survey was anecdotal and required proper experimental studies to provide a better understanding of contact lens wear in the workplace.
In the early 1970s, various organizations including the National Society to Prevent Blindness (now called Prevent Blindness America) and the American National Standards Institute (ANSI) joined the debate by attempting to address the safety concerns associated with contact lens wear in the work environment. Uncertainty and lack of research prompted the National Society for the Prevention of Blindness in 1972 to recommend that workers should not wear contact lenses in certain workplaces.
![]() |
|
Figure 1. less than 0.0001 percent of UV light transmits through a welder's shade number 10
tint. |
|
Arc Welding In the 1960s several unsubstantiated reports intimated that rigid contact lenses had "fused" to eyes during arc welding, and such reports have surfaced in the general media periodically over the decades. Unfortunately, such sensationalized reports have contributed to the development of some inappropriate safety policies prohibiting the general use of contact lenses in industry.
One of the first reports gave an account of an electrical engineer at Bethlehem Steel Corporation in Baltimore, MD, who was exposed to an electrical explosion. He was wearing safety glasses over his contact lenses, but it was first reported that when he removed his contact lenses "large amounts of dried cornea came off with each lens."
Scientific studies have not been able to demonstrate the mechanism by which a contact lens could fuse to the cornea, nor have they been able to replicate this phenomenon. In fact, a study about UV light has shown that less than 0.0001 percent of UV light transmits through a welder's shade number 10 tint (Figure 1). Such transmission of UV and other light could not cause fusion.
Some have suggested that temperature change related to arc welding is the mechanism for contact lenses "fusing" to the cornea. A 1979 study showed that low energy welding sources can cause an increase in contact lens temperature, especially in thicker lenses. Additional experiments have shown that infrared heaters may also increase the temperature of hydrogel contact lenses. The heat produced from these types of radiation exposures may dehydrate the lens, although it is unlikely that the lens would fuse with the cornea.
However, toxic fumes that contain particulates are often a byproduct of welding. Therefore, workers in these environments should wear GP contact lenses only when they can easily and safely cease operations before these byproducts incapacitate them. In 1983, the Contact Lens Association of Ophthalmologists (CLAO) released a policy statement on arc welding and contact lens wear that said arc welding is not associated with an increased risk for ocular damage.
Chemical Agents Chemical work environments could pose a threat to lens wearers through direct physical contact of the agent with the ocular tissues and exposure to noxious fumes. A chemical may become trapped behind a contact lens and extend exposure time, especially if the lens prevents water or other liquid from diluting the chemical during irrigation.
The eye usually responds to chemical exposures with protective mechanisms such as increased blinking and lacrimation, which dilute and help wipe away the chemical agent. The naturally occurring enzymes and buffering agents in the preocular tear film (POTF) help reduce potential damage to the ocular surface. A 1975 study used animal models to simulate chemical accidents to the eyes of hard contact lens wearers. Researchers fit one eye with a hard contact lens and the other served as the control. Results showed that the eye wearing the lens was more protected from the chemical exposure than the control eye.
In 1982 a study exposed rabbit eyes with and without contact lenses to alkalis, acids and to chemical vapors. The results showed that while hydrogel contact lenses helped protect the eyes from acids, they offered little protection from strong alkalis because the corneal damage with direct alkali exposure appeared equal for eyes with and without hydrogel contact lenses.
These studies also revealed that hydrogel materials uptake the chemical vapors and release them into the air over time, which indicates that although contact lens wear could result in longer exposures to chemicals, the exposure concentrations are generally lower than those found with direct contact of the vapor to the ocular surface. However, because of the longer exposure, industrial workers should not wear contact lenses on an extended wear schedule and they should routinely clean the lenses and replace them at shorter intervals than for typical contact lens patients.
Gases and vapors associated with noxious chemical agents conceivably could pose a threat to soft contact lens wearers by direct diffusion through the contact lens to the ocular surface. Many noxious fumigants (allyl disulfides found in onions and some tear gases) are insoluble in water, so soft contact lenses may shield the ocular surface from such agents. Another 1982 study examined the effect of sulphur dioxide on hard contact lens wear. It found that concentrations up to 50ppm result in small increases in tear production compared to an 83 percent increase in tear production in those not wearing contact lenses.
The effects of gases and vapors on professionals such as hairdressers and painters remains unknown in terms of fume adherence and absorption into contact lenses.
![]() |
|
Figure 2. Metallic particle embedded in a contact
lens. |
Foreign Bodies and Mechanical Trauma Flying particles or foreign bodies can cause severe mechanical trauma to the ocular surface both with and without contact lens wear. Early 1980s studies investigated the effects of metallic particles on hydrogel contact lens wear in animal eyes. Human studies found that hydrogel lenses could be worn safely in this environment because no additional risk of ocular damage existed.
Studies in which researchers fit anaesthetized rabbit eyes with hard or soft contact lenses and then exposed them to burning grit particles found that both hard and soft contact lenses minimally protected the ocular surface, which generally developed superficial wounds after exposure to flying debris. The soft lenses sustained more extensive damage from both large and small particles (Figure 2). The researchers concluded that soft contact lenses do not exacerbate any potential injury associated with mechanical risks. With larger particle exposure, the study found that low water hydrogels provided some protection to corneal penetration, but polymethylmethacrylate (PMMA) lenses not only provided no protection, but may also have caused extra damage because flakes from the rigid lens may have become embedded in the cornea after lens breakage. With proper eye and face protection, however, hard contact lens wear should not create an additional hazard around flying particles.
Workers should wear rigid contact lenses with caution around dust and smoke particles because the particles' entry behind the lens could visually incapacitate the workers and place them at risk of further injury. This is especially true in hazardous environments such as when welding or working at heights. If the worker cannot safely call "timeout" and easily cease operations to remove the contact lens and attend to the foreign body, then it's probably better to limit rigid lens use.
Physical Agents Several studies have examined the effects of heat and cold, drafts and radiation on contact lens wearing eyes. A 1982 study examined the effects of extreme cold and drafts for a period of several hours on the ocular tissues of rabbits wearing hard contact lenses and found only superficial damage. Studies show that exposure to infrared heaters during contact lens wear results in no additional risk of ocular damage.
Numerous studies indicate that UV-absorbing contact lenses offer some protection to the cornea and perhaps the internal ocular structures. Soft lenses generally protect better than gas permeable (GP) lenses because the large diameter of soft lenses covers the entire cornea and limbus, where the corneal stem cells are located. In fact, some would suggest that soft lenses offer better protection to the ocular surface and internal ocular structures than spectacle lenses because radiation may circumvent the spectacle lenses. However, in environments or situations with intense UV radiation, workers should substitute neither contact lenses nor spectacles for safety goggles or a face shield with welding filter of the proper shade number. With appropriate eye protection, contact lens wear during most radiation exposures, including arc welding, is considered safe. Of concern with welding, however, are the fumes with particulate that often result. This environment may introduce foreign bodies behind a hard lens, visually incapacitating the welder. This would create a hazardous situation because the welder would be visually limited while holding a hot, electrically charged electrode.
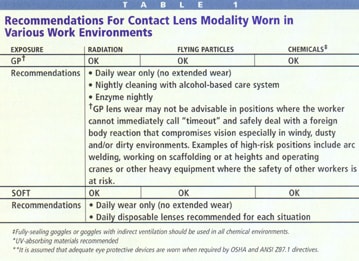
Table 1 shows some of our general guidelines for contact lens selection with various workplace hazards, and Figure 3 details our recommended guidelines for the prevention and intervention of work-related contact lens injuries.
![]() |
|
Figure 3. Recommendations for safe contact lens wear in industrial work
environments. |
|
Governmental Directives
Many studies have supported safe contact lens wear in the work environment by evaluating the physiological responses of animal ocular tissues to exposures. Although these studies help provide a basic understanding of the interaction between the ocular tissues and contact lenses in the work environment, we must consider the human element involved in contact lens wear. This includes factors such as individual reaction times, the blinking response, wearing eye protection, avoiding dangerous situations and being able to remove contact lenses quickly and safely.
Therefore, governmental groups developed policies and directives regarding contact lens use in general and specific work environments. The three primary governmental groups involved are the US Food and Drug Administration (FDA), ANSI and the Occupational Safety and Health Administration (OSHA) in the Department of Labor.
FDA Until the early 1970s, the FDA did not regulate contact lenses and solutions. With the advent of soft hydrogel lenses, the FDA decided to regulate them in the public's interest. Because no regulatory mechanism specific to medical devices existed at that time, the Bureau of Drugs first regulated contact lenses and their accessory solutions as new drugs, which required approval of a New Drug Application (NDA) before commercial distribution could occur.
In 1976, the US Congress enacted Medical Devices Amendments to regulate medical devices differently from drugs, and the Bureau of Medical Devices (now the Center for Devices and Radiological Health) was established within the FDA. Some medical devices -- including contact lenses and solutions -- that the Bureau of Drugs had once regulated as new drugs became "transitional." This put contact lenses and solutions in the strictest device regulation group, Class III, where they remained until down classification to Class II began for some in 1993 (Class I involves general controls, Class II special controls and Class III premarket approval [PMA]).
The FDA's principal objective is to provide a reasonable assurance of safety and efficacy of drugs or devices both before and after companies may market them to the public. Based on its general history and potential risk/benefit relationship, the FDA places a product in one of the three classes. Class II special controls determine the substantial equivalency of investigational contact lenses or solutions with similar and previously approved products. Class II requires both non-clinical testing (microbiology and toxicology) and clinical testing.
Class III also requires appropriate non-clinical and clinical testing, but it involves a longer clinical testing duration and a greater number of subjects than Class II. As in Class II, Class III lenses are compared with similar, previously approved products to prove substantial equivalency. In addition, Class III lenses must also demonstrate independent safety and efficacy. Only extended wear contact lenses now fall under Class III, as do contact lens solutions that feature certain different chemistry than those on the market.
The FDA considers Class III studies to involve "significant" risk, while Class II studies are "non-significant" risk. Class III devices receive PMA while Class II devices receive clearance under a 510K premarket notification.
While state laws and licensure govern practitioners, the FDA regulates manufacturers. The approved labeling section that appears on and/or is inserted in the packaging describes the FDA's approval terms for a given product.
Although the FDA does not directly govern practitioners, prescribing or recommending devices in any way that differs from FDA guidelines and labeling can result in legal problems. In essence, FDA's guidelines and labeling constitute its policy both for general use and specific industrial use of contact lenses.
ANSI and NIOSH The ANSI Z87.1-1989 policy regarding the use of contact lenses in industry states, "Contact lenses themselves do not provide eye protection in the industrial sense." A revised version of the ANSI Z87.1 standard has just been published. Both the old and new policies require that workers who wear contact lenses must wear the same eye protecting devices as workers who don't wear contact lenses. Contact lens wearers should take extra precautions when delay in taking the appropriate action (flushing the eyes with water or removing the lenses) may happen because of the work circumstances or because a worker is more concerned with saving the lenses than with saving his eyes.
The National Institute for Occupational Safety and Health (NIOSH) also has a policy statement outlining the use of contact lenses in the chemical industry. A summary of their most recent policy statement suggests, "In general, a lack of injury data exists to clearly indicate that contact lens wear should be restricted when working with hazardous chemicals; however, appropriate eye protection is always necessary."
OSHA The government enacted the Occupational Safety and Health Act in 1970 to help provide safer working conditions for the then more than 100 million US workers. This national health and safety law established OSHA. It required employers to provide workers with safer work environments that are free from known risks associated with injury and it required employees to abide by all health and safety rules that apply to their jobs. OSHA currently recommends against contact lens use when working with acrylonitrile, methylene chloride, dibromo-3-chloropropane, ethylene oxide and methylene dianiline.
One Bureau of Labor study found that up to 60 percent of workers who suffered eye injuries were not wearing eye protection. About 70 percent of the accidents resulted from flying or falling objects or sparks striking the eye; chemical exposures caused about 20 percent of eye injuries. Personal protective equipment (PPE) is manufactured and designed to protect individuals at home or work from serious injuries. Examples of PPE include face shield, safety glasses, hard hats, safety shoes, goggles (Figure 4), coveralls, vests, earplugs and respirators.
OSHA-published requirements are in Title 29 of the Code of Federal Regulation (CFR), Part 1910-Subpart I. In general, these requirements mandate that employers conduct assessments of the workplace for hazards that would necessitate the use of PPE and provide workers with the appropriate PPE for the work hazard. Employees often require training to educate them about appropriate times for PPE wear and its proper use. OSHA also recommends that employers provide emergency eye washes in strategic locations.
![]() |
|
Figure 4. Safety goggles may protect the eyes from
injury. |
Organizations' Position Statements
Many organizations have developed policy statements regarding contact lens wear in industrial environments. These organizations include the American Optometric Association (AOA), the American College of Occupational and Environmental Medicine (jointly with the American Academy of Optometry), the Contact Lens Association of Ophthalmologists (CLAO) and Prevent Blindness America (Table 2). The American Academy of Optometry, American Medical Association and American Public Health Association have no policy statements.
The AOA recently published an Occupational Vision Manual to educate practitioners about eye health and safety in the work environment. The manual provides recommendations regarding occupational eye injuries, worker vision assessments, ocular protection and medico-legal and ethical issues associated with standards and regulations and contact lens use in the industry.
When you fit contact lenses for industrial workers, address the lens wear issues for each worker's specific environmental situation. This is important because the type of work and hazards a patient experiences influences the type of contact lens and wearing schedule that he should use.
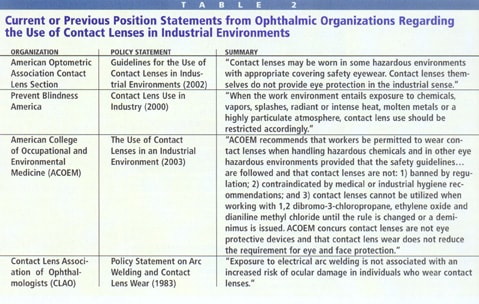
Corneal Refractive Surgery
Most governmental directives and organizational position statements were issued before the large scale use of corneal refractive surgery. As the number of corneal refractive surgery procedures continues to grow, advise your postoperative patients how to protect their eyes.
Radial keratotomy (RK) compromises globe integrity in resistance to blunt or mechanical trauma. Research indicates that post-RK eyes rupture from significantly less force than what would rupture normal eyes. RK eyes generally rupture at incision sites. Reports indicate that at least 28 globes have ruptured in RK patients.
LASIK flap dislocations are a more common complication and usually occur during the first few months following surgery. However, one report noted that flap dislocations have occurred up to 38 months postoperatively with direct corneal trauma. Mechanical traumas to the ocular surface may pose as much hazard to postoperative LASIK patients as to contact lens wearers.
To our knowledge, no studies exist that examine how radiation and chemical exposures affect the healing of postoperative LASIK corneas. It is imperative that employers, employees and health care workers recognize the potential risks to postoperative refractive surgery patients and the potential hazards in their workplace to ensure that post-LASIK patients receive appropriate safety protection.
Conclusions
With proper precautions such as identification of safety hazards and the wear of appropriate safety protective devices, contact lens wear may be safe and even offer potential advantages over spectacles in many work environments. Postoperative refractive surgery patients may pose a new challenge for safety officers and industrial employers, as little is known about the effects of chemical, mechanical or radiant injuries to these patients.
Dr. Nichols is a senior research associate at The Ohio State University College of Optometry.
Dr. Good is a professor of Clinical Optometry at the Ohio State University College of Optometry and Diplomate in the American Academy of Optometry Section on Public Health and Environmental Vision.
References are available upon request. To receive references via fax, call (800) 239-4684 and request document #99. (Have a fax number ready.)