LENS MATERIALS
Comfortable Contact Lenses: A Case of Mission Impossible?
Lens material advancements attempt to improve dry eye symptoms to keep patients wearing lenses.
By Lyndon Jones, PhD, FCOptom, FAAO; Kara Menzies, BSc, MSc; & Lakshman Subbaraman, PhD, BSOptom, MSc, FAAO
![]() Dr. Jones is associate director of the Centre for Contact Lens Research and a professor at the School of Optometry at the University of Waterloo. He has received research funding from Alcon, AMO, B+L, Ciba Vision, CooperVision, Johnson & Johnson, and Menicon. ![]() Kara Menzies recently completed her MSc in Vision Science at the School of Optometry at the University of Waterloo. ![]() Dr Subbaraman is currently a post-doctoral researcher at the Chemical Engineering Department, McMaster University. |
The first comprehensive study investigating contact lens dropout was conducted almost 20 years ago (Weed et al, 1993) and indicated that end-of-day dryness and discomfort was the most common reason for ceasing contact lens wear, with approximately 50 percent of wearers citing this as their primary complaint with lenses. Despite the advances in contact lens materials since that time, patients are still “dropping out” of contact lens wear as a result of discomfort (Pritchard et al, 1999; Young et al, 2002; Richdale et al, 2007; Chalmers et al, 2009). Studies suggest that 22 percent to 24 percent of patients permanently discontinue contact lens wear (Pritchard et al, 1999; Richdale et al, 2007) and that contact lens wearers are 12 times more likely than emmetropes and five times more likely than spectacle wearers are to report dry eye symptoms (Nichols et al, 2005).
Studies recently conducted at the Centre for Contact Lens Research to assess compliance with replacement frequency of daily disposable and silicone hydrogel lenses (Dumbleton et al, 2009; Richter et al, 2010) indicate that 47 percent of patients in the United States and 55 percent of patients in Canada reported that their lenses became less comfortable later in the day—numbers that are depressingly close to those published in the 1990s. These studies also indicate that comfortable wearing time, even with the most modern soft lens materials, is only about 10 hours per day for many patients, which does not meet the lifestyle requirements of most patients. So, have we improved comfort with contact lenses at all over the past 20 years?
Lens comfort is influenced by many factors, including those related to individual patients, care regimen and lens material (Fonn, 2007). This article will concentrate on various approaches taken by companies to enhance lens material comfort. But remember, factors such as lens design and fit also play a critical role in enhancing comfort, as even the most well-developed material will be uncomfortable if lens fit, edge contour, thickness, and overall design are not optimized (Young et al, 1993; Dumbleton et al, 2002; Young and Coleman 2001).
Over the past decade, most developments in soft lens materials have occurred in those that are now the most commonly fit in most markets: single-use daily disposable and reusable silicone hydrogel materials (Morgan et al, 2010). Within these materials, the major changes can be broadly categorized into attempts to adjust bulk properties, surface properties, or the properties of the packaging solution.
Bulk Material Properties
One current area of great interest is biomimesis or bioinspiration, with a recent special issue of Contact Lens Spectrum (Special Edition 2010) being dedicated to this topic. Biomimicry or biomimetics involves examining nature’s systems and processes and then exploiting these to solve human problems. The terms biomimicry and biomimetics come from the Greek words “bios” (life) and “mimesis” (to imitate). The first soft lens material to use such a process is arguably the non-silicone hydrogel material omafilcon A used in the Proclear series of lenses (CooperVision). The material combines polyHEMA and synthetically produced molecules of phosphorylcholine (PC). PC is a zwitterionic phospholipid found on the outer surface of various cell membranes and has been used for more than 20 years as a synthetic polymerbased coating on drug-eluting stents to prevent recurrence of coronary artery narrowing (Hayward and Chapman, 1984; Iwasaki et al, 1997). The omafilcon A material was developed in the late 1990s as a spinoff from this blood compatibility work, and studies have shown that it exhibits low levels of bulk dehydration and tear film deposition (Young et al, 1997; Hall et al, 1999; Lemp et al, 1999).
One of the factors often stated as being important in contact lens-related dry eye is bulk material dehydration, as dryness symptoms appear to occur more frequently in soft lens wearers whose lenses undergo greater dehydration (Efron and Young, 1988). Potential factors that may explain dehydration-induced discomfort include increased lid-lens interaction through alterations in material front-surface wettability or the development of corneal epithelial staining due to pervaporation and desiccation (Pritchard and Fonn, 1995; Orsborn and Zantos, 1988). Many studies have shown that dehydration is influenced by a number of factors, including the surrounding environment (Brennan et al, 1988), water content (with higher-water-content materials dehydrating to a greater extent) (McConville and Pope, 2001; Jones et al, 2002; Gonzalez-Meijome et al, 2007), water binding properties (Larsen et al, 1990), and thickness (with thin lenses dehydrating more compared to thick lenses) (Helton and Watson, 1991). Most studies indicate that traditional polyHEMA-based hydrogel materials dehydrate to a greater extent and at a faster rate compared to silicone hydrogel lens materials (Jones et al, 2002; Gonzalez-Meijome, et al, 2007), and higher-water-content materials are more likely to be associated with dry eye symptoms (Nichols and Sinnott, 2006; Ramamoorthy et al, 2008; Ramamoorthy et al, 2010). In addition, several studies now indicate that silicone hydrogel materials, which are all relatively low in water content, may prove beneficial in managing patients who have symptoms of ocular dryness (Chalmers et al, 2009; Riley et al, 2006; Schafer et al, 2007; Young et al, 2007; Chalmers et al, 2008; Dumbleton et al, 2008; Ousler et al, 2008).
Summarizing all of these data, it would seem compelling to believe that bulk dehydration is directly linked to comfort and that developing materials with low dehydration rates would result in enhanced lens comfort. However, several studies show a poor direct relationship between bulk dehydration and wearing comfort (Pritchard and Fonn, 1995; Nichols and Sinnott, 2006; Fonn et al, 1999), and it may well transpire that higher-water-content lenses induce lower comfort scores not as a result of bulk water loss/dehydration but rather due to alterations in surface wetting, surface dehydration, or surface deposition (Nichols and Sinnott, 2006). Much work remains to unravel why lower-water-content materials tend to result in enhanced comfort scores.
Surface Material Properties
The elusive search for enhanced lens comfort has resulted in a number of manufacturers attempting to use sophisticated chemistry to try to produce more highly wettable surfaces. These include a variety of approaches, but can broadly be broken down into three concepts.
Surface Treatments This idea largely arose from silicone hydrogel lenses that are difficult to “wet” due to the incorporation of siloxane groups. Silicone hydrogels provide high levels of oxygen transport but are relatively hydrophobic. Various approaches have been used to convert the lens materials into wettable, clinically viable lenses (Tighe, 2006; Tighe, 2004; Jones et al, 2006). PureVision (balafilcon A, Bausch + Lomb) lenses are surface treated in a reactive gas plasma chamber that transforms the silicone components on the surface of the lenses into hydrophilic silicate compounds (Tighe, 2004; Valint and Grobe, 2001; Grobe et al, 1999; Lopez-Alemany et al, 2002). Glassy, discontinuous silicate “islands” result (Lopez-Alemany et al, 2002; Gozalez-Meijome et al, 2006; Teichroeb et al, 2008), and the hydrophilicity of the transformed surface areas “bridges” over the underlying balafilcon A material.
For its Air Optix Night & Day Aqua (lotrafilcon A) and Air Optix Aqua (lotrafilcon B) lenses, Ciba Vision uses a gas plasma technique to apply an extremely thin, uniform, high-refractive index, 25nmthick hydrophilic plasma coating on the lens surface after manufacturing. The coating is significantly more wettable than the underlying material (LopezAlemany et al, 2002; Gozalez-Meijome et al, 2006; Teichroeb et al, 2008; Nicholson, 2003). Menicon uses a combined approach of plasma polymerization and plasma coating to improve wettability of its Premio lens (asmofilcon A) (Jones, 2007).
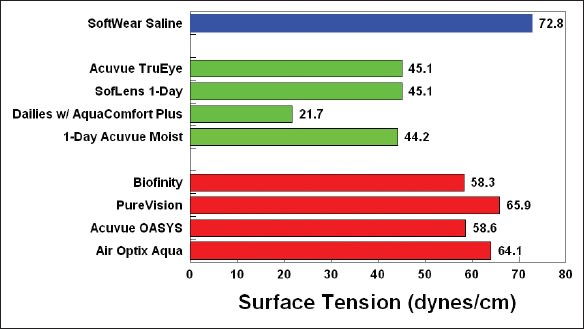
Figure 1. Surface tension values for the blister pack solutions of various daily disposable and reusable silicone hydrogel lenses, in comparison with a saline control.
Internal Wetting Agents Vistakon’s Acuvue Advance (galyfilcon A), Acuvue Oasys (senofilcon A) and 1-Day Acuvue TruEye (narafilcon B) feature technology that renders the lens wettable without the need for modification. (Jones et al, 2006; Teichroeb et al, 2008, Steffens and Schnider, 2004; French, 2008). The materials contain a permanently embedded high-molecular-weight wetting agent, polyvinyl pyrrolidone (PVP), that helps to achieve a highly wettable, smooth lens (Sheardown and Liu, 2009). Hydraclear technology is used to embed the internal wetting agent in the Acuvue Advance lens. Acuvue Oasys is made using Hydraclear Plus technology (implying that more PVP is probably incorporated), and Hydraclear 1 technology is used to make the Acuvue TruEye lens. Published results to date for the 1-Day Acuvue TruEye lens have been impressive, with ocular comfort and physiological performance being similar to that of spectacle wearers (Morgan et al, 2009).
CooperVision’s Biofinity (comfilcon A) (Jones, 2007) and Avaira (enfilcon A) feature technologies that incorporate their siloxane components in such a way that the materials are “naturally wettable,” again without the need for surface treatment.
The concept of employing internal wetting agents has also been exploited by Vistakon in its 1-Day Acuvue Moist daily disposable. The lens incorporates PVP as a wetting agent into the well-established etafilcon A material through a proprietary technology (Lacreon) to produce a more wettable version of the material (Veys and Meyler, 2006; Sulley and Meyler, 2010). This wetting agent is also permanently embedded and does not leach out from the lens over the course of the day (Veys and Meyler, 2006; Sulley and Meyler, 2010; Sheardown et al, 2006).
Migratory Polymers The Ciba Vision Dailies series of lenses (the most recent being Dailies AquaComfort Plus) is manufactured in nelfilcon A, which is based on polyvinyl alcohol (PVA) (Morris, 2008). PVA is commonly found in artificial tear formulations such as Hypotears (Novartis), Refresh (Allergan), and Blink (AMO). In the original formulation, the PVA was polymerized into the lens material to N-formylmethyl acrylamide and was termed as being “functionalized.” The newest formulation has functionalized PVA in the lens matrix as well as excess non-functionalized PVA that floats free in the lens matrix (Peterson et al, 2006). This non-functionalized PVA migrates to the lens surface and is slowly released from the lens over the course of the day (Morris, 2008; Winterton, 2007). As a result, the lens surface maintains its wettability and releases a moisturizing agent into the tears over the course of the day (Peterson et al, 2006; Winterton et al, 2007; Nichols, 2007; Menzies et al, 2010; Wolffsohn et al, 2010).
Packaging Agents
Another area that has attracted much attention over the past two to three years relates to the impact of adding various lubricating agents (such as HPMC) or surface active agents (such as poloxamine) to the blister pack solution (BPS) in which the lenses are stored in an attempt to enhance lens surface wettability following lens application. This is obviously of greatest impact for daily disposable lenses, although the concept of using the BPS to positively impact lens comfort has also been adopted by manufacturers of reusable silicone hydrogel materials, particularly in the Air Optix Aqua and Air Optix Night & Day Aqua lenses from Ciba (Nash et al, 2008; Gabriel and Nash, 2009). Several publications have discussed this concept (Morris, 2008; Nichols, 2007; Menzies et al, 2010; Pruitt et al, 2007; Cairns, 2007; Cairns et al, 2009; Mack, 2009; Pence, 2009). Two recent studies by Menzies et al (2010) have described the variations in the physical properties of these BPSs—such as pH, viscosity, surface tension and osmolality—which indicate how different they can be, depending on their composition.
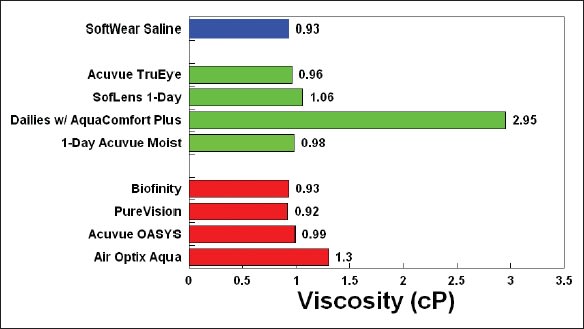
Figure 2. Viscosity values for the blister pack solutions of various daily disposable and reusable silicone hydrogel lenses, in comparison with a saline control.
The results indicate that the pH values of the BPSs are all around neutral pH, and that while the osmolality values do differ, they tend to be fairly similar for products from the same manufacturer. The largest difference among products appears to be in the values for surface tension and viscosity, as evidenced by Figures 1 and 2. The surface tension of water is approximately 72 dynes/cm, and adding surface active agents will reduce this value. Figure 1 suggests that all of the products described have some degree of surface active agent within the BPS, as the surface tension values are all lower than both water and saline. The lowest surface tension value is that of the Dailies AquaComfort Plus lens. This is attributable to the combination of hydroxypropyl methylcellulose (HPMC) and polyethylene glycol (PEG) in the blister pack, and the release of non-functionalized PVA from the lens material into the BPS after manufacture (Winterton et al, 2007; Pruitt et al, 2007). The viscosity of water is approximately 1 centipoise (cP), and adding more viscous agents will raise this value. Figure 2 indicates that the most markedly different BPS viscosity is also that of the Dailies AquaComfort Plus lens, once again due to the triple combination of HPMC, PEG, and PVA (Winterton et al, 2007; Pruitt et al, 2007).
It is likely that this approach of varying the BPS composition to enhance initial wearing comfort will continue, particularly for daily disposable lenses.
Summary
The elusive quest for all-day comfort appears destined to continue for some time, but there does seem to be some hope, as several studies have confirmed that refitting patients into modern, welldesigned silicone hydrogel materials have resulted in improved end-of-day comfort compared with their habitual, traditional lens materials (Riley et al, 2006; Schafer et al, 2007; Young et al, 2007; Chalmers et al, 2008; Dumbleton et al, 2008). Companies continue to develop new approaches to deal with end-of-day comfort issues, and we hope the next 10 years will bring new materials with surfaces that provide similar levels of comfort to that seen in non-lens wearers—or maybe even provide a protective effect such that contact lenses provide greater comfort than that measured without a lens in place. Or is that really a case of Mission Impossible? CLS
For references, please visit www.clspectrum.com/references.asp and click on document #176.