Our focus this month is on specialty lens polymer manufacturer Acuity Polymers. I recently had the pleasure to speak with Jonathan Jacobson, CEO and commercial vice president.
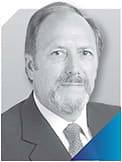
Mr. Jacobson, please tell us about your company in terms of its history and direction.
Acuity Polymers is based in Rochester, NY. The company formed following the consolidation of two leading lens material manufacturers and the resulting concern among specialty laboratories with regard to access to quality materials at a fair price. During the late spring and summer of 2015, President/COO Jim Bonafini, Vice President of Technical Services Daniel Bell, and I were approached independently by labs in the United States and worldwide about creating a new polymer company. It was at this time that the three of us came together to found a polymer company that could produce the same high-quality materials that labs had been using successfully for years.
The first Acuity Polymers materials that we developed are actually clones of existing materials that are no longer covered by patents. We’ve effectively reverse engineered the most popular GP lens materials and then applied state-of-the-art manufacturing methods to produce what we and others consider to be improved versions of the original products.
Our goal is to bring innovation and research and development back into the custom space. There have been some interesting developments with surface coatings and treatments, and that’s nice to see. But I feel that we also need to work at improving the materials themselves, particularly if we’re going to have ever-larger GP lenses being fit.
Tell us about any new products or new developments in which Acuity Polymers is involved.
We’re currently working on what will be the highest-Dk GP material on the market when it is cleared. This material, which will come to market in the first half of next year, is aimed primarily at the large-diameter as well as the myopia control lens segments for which higher gas permeability is very beneficial.
We’re also developing a mid-Dk latheable silicone hydrogel material that is designed to have predictable and stable expansion characteristics so that the lens can be offered in a quarterly replacement format using annual supply packaging. This product is currently undergoing manufacturing trials.
We also have a lens care product in development; we see the importance of a system of lenses and lens care, in which you have products that are manufactured to be complementary with one another.
Tell us your vision for the contact lens field in the short term (less than 5 years) and in the long term (20 years from now).
In the short term, we are expecting to see an upturn in GP lens fitting for both irregular and more normal corneas driven by large-diameter, hyper-Dk lenses that are surface treated to improve comfort. I believe that we’re going to see an increased use of software to improve first-fit success with these lenses, including software that can constantly update and learn from itself.
I think that we’ll see an increase in use of custom rigid, custom soft, and hybrid lenses for myopia control as well as for presbyopia.
In the longer term, we expect to see multi-modulus lenses with progressively decreasing moduli as you move from the center (which will be stiff) to the edge (which will be flexible). I also think that lenses made with 3D printing could be in our grasp within that time frame. Imagine instead of lathing complex geometry lenses, high-capacity 3D printers would print lenses. Instead of ink, you might have 10 different monomer/polymer mixtures used in a printing process. Probably very far-fetched right now, but people are conceiving it as we speak. CLS